At around 7:21pm, on May 7, 1937, the German passenger airship, LZ 129 Hindenburg dropped its mooring lines in preparation for landing at Naval Air Station, Lakehurst, United States. Except for strong headwinds which slowed its progress, the entire trip from Frankfurt was uneventful. A few minutes later, some witnesses saw a part of the fabric fluttering indicating the possibility of a gas leak. Within 37 seconds, the 237m long craft was engulfed in flames and came crashing to the ground resulting in 35 deaths and causing severe injuries and burns to the other 97 people on-board.
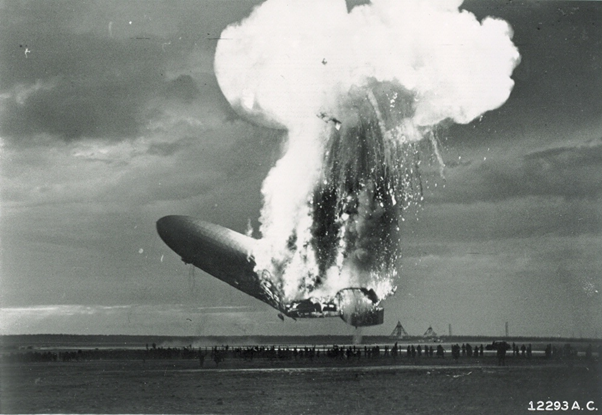
While multiple theories have been proposed as to the cause of the initial ignition, the massive fireball would not have been possible if it wasn’t for the 140,000 cubic metres of Hydrogen that was used to keep the craft afloat.
The Hindenburg disaster was covered remarkably well on camera by 1937 standards, and has since become the poster child of the dangers of Hydrogen.
While the importance of Hydrogen safety cannot be overstated, sometimes the myth around it blurs the line between caution and paranoia.
In this article, I discuss the specific properties of Hydrogen that make it unique as a fuel, and intend to dispel the myths around the safe use of this fuel by highlighting some key measures that can mitigate most of the risks.
Hydrogen is everywhere
Making up 73% of all matter in the universe, Hydrogen is the most abundant element in existence. However, only minute traces of gaseous Hydrogen are found in Earth’s atmosphere (0.6 parts per million), because earth’s gravitational pull is not strong enough to retain these extremely light molecules (14 times lighter than air). It is the lightest gas, with the smallest molecular size.
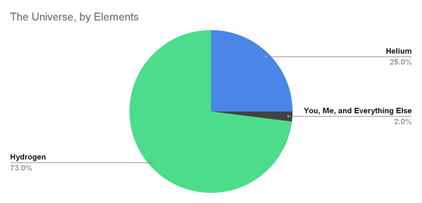
Due to its position as the first element in the periodic table, it exhibits almost all chemical properties to the extreme. The unique properties of Hydrogen give rise to unique characteristics, and therefore special ways are needed to handle it safely.
Low Ignition Energy – Flammability
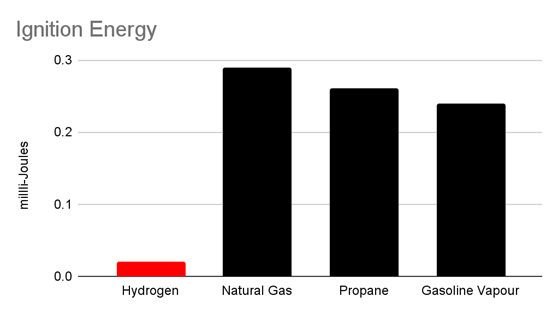
Hydrogen is one of the most flammable gases known. The minimum ignition energy of a Hydrogen-Air mixture is 0.019 mJ - significantly less than that of other fuels like petrol, methane, propane, and butane, which are typically on the order of0.1 mJ or more.
This makes Hydrogen prone to ignition through low energy sparks, even the ones caused by electrostatic discharge. To handle this risk, specific design considerations which have already proven successful for other explosive gases should be established.
- Proper Electrical Grounding: Electrical Grounding is a critical safety consideration in any industrial setting. However, when it comes to Hydrogen, the grounding requirements become more crucial. Grounding helps dissipate charges which might otherwise build up leading to an electrostatic discharge.
- Explosion-Proof enclosures: The possibility of an explosion can be reduced by using Explosion-proof enclosures around powered components like Instruments, Motors, Junction Boxes, and Solenoids. In case of an ignition caused by any electrical spark, the flame is contained inside the enclosure.
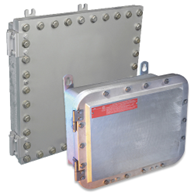
- Intrinsically safe components: Electronic components can be made intrinsically safe by introducing a barrier and using special modules and techniques that lower the energy available to the component below what is required to produce a spark.
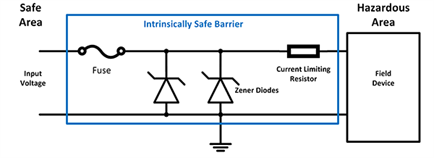
Wide range of Explosive Mixtures
Hydrogen is explosive over a wider range of mixture ratios in air than most other fuels. A mixture of anywhere between 4% to 75% Hydrogen in air is considered explosive. This range is significantly wider than that of other fuels like petrol (1.2% to 7.1%), methane (5% to 17%), or butane (1.8% to 8.4%). During electrolysis, this problem is exacerbated due to the evolution of pure Hydrogen-Oxygen mixtures wherein the range widens from 4% - 75% (in Air) to 4% - 95%(in O2). Continuous monitoring along with preventive measures are required to mitigate this risk.
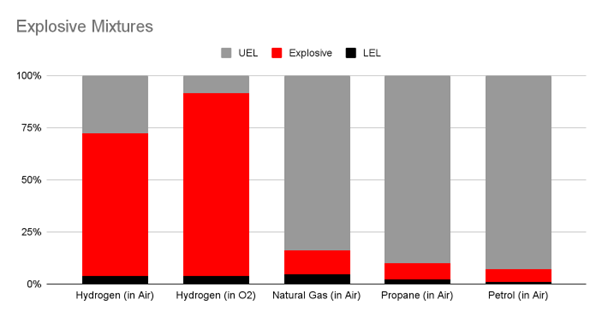
- Continuous monitoring of H2 / O2 ratios: H2% in O2 stream, and O2% in H2 stream should be continuously monitored and complete system shutdown followed by purging should be commenced if the concentration of any mixture crosses the boundary into explosive limits.
H2% in O2 can be monitored through binary gas analyzers employing thermal conductivity principle or the speed of sound principle. O2% can be monitored through paramagnetic or electrochemical sensors. Use of Zirconia sensors for O2 monitoring is not recommended due to the tendency of those sensors to heat up.
- Flame Arrestors: Flame Arrestors should be used wherever Hydrogen from the process is being released into an area or system which has the possibility of causing ignition. Generally, flame arrestors are used in all Hydrogen and Oxygen vents in an Electrolysis process (called End-of-Line Flame Arrestor). They are also used when the gas is taken into a system where it is not feasible to completely eliminate the chances of ignition occurrence.
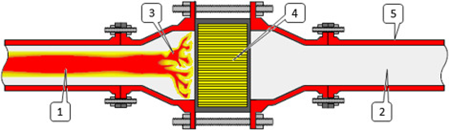
(Image Credit: Plant Design and Operations, Ian Sutton, Sutton Technical Books)
Small Molecular Size – Easy chance of leakage
The Hydrogen molecule is extremely small. For a leak of the same size, the amount of Hydrogen that would escape through the leak is the highest amongst all gases. Leakage rates are 50x higher than water, and around 10x higher than Nitrogen. Materials and fittings which are considered leak tight for most other applications may not be suitable for Hydrogen. To address this challenge, multiple tests are available which can be used to ascertain the leak tightness of components used in Hydrogen Service.
- Sniffing Test: The object under test is filled with a mixture of Hydrogen and Nitrogen, just outside the explosive limit (1:20 ratio). A handheld hydrogen sensor is used to check around the possible leakage points. This is a cheaper alternative to the more accurate Helium Leak test.
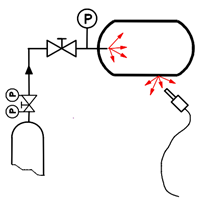
- Helium Leak Test: Helium is used as tracer gas in concentrations as low as 0.1 parts per million. Being the lightest inert gas, helium penetrates microscopic leaks rapidly, and doesn’t react with the object under test. Helium is also rare in the atmosphere - therefore, detection is not complicated by contamination from ambient air.
This method is extremely sensitive and leaks as small as 5 x 10-10 Pa.m3/s can be detected if a vacuum is pulled inside the test object.
Small Molecular Size - Permeates through Vessel Walls
Hydrogen can permeate through solid vessel walls over time, even the ones made from stainless steel. This problem exacerbates at higher pressures. Hydrogen is typically stored at pressures ranging from 300 to 1000 bar. Although it can be stored in metal vessels when leakage is not a primary concern, for long term storage and transportation, special materials are utilized for construction.
- Composite Materials: Hydrogen storage vessels, especially the ones meant for long term storage or transportation are ideally made of special composite materials like carbon-fibre reinforced plastic, with HDPE liners which act as hydrogen permeation barriers.
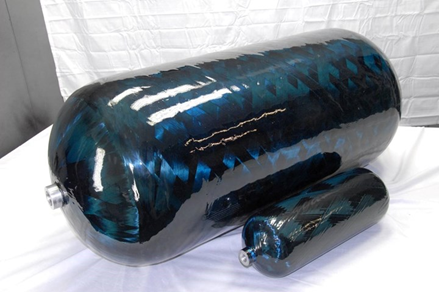
Small Molecular Size - Hydrogen Embrittlement
The small size of the hydrogen molecule allows Hydrogen to diffuse into interstitial spaces in Metallic lattices or polymers causing a reduction inductility over time. This lowers the stress required for the formation and propagation of cracks, making the material brittle over time.
Therefore, proper selection of materials in Hydrogen service is critical.
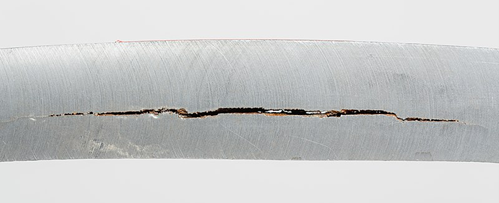
- Stainless Steels: Stainless steel with hardness less than HRC 32 are considered less susceptible to embrittlement. SS316 is considered the most suitable.
- Standardized susceptibility tests: ASTM F1459 prescribes tests using a diaphragm made of the Material under test subjected to differential pressure. ASTM F1624 prescribes standard test methods to determine embrittlement thresholds for steels by incremental loading. A specified loading rate is applied which is equal to or lower than the actual loading that will be experienced by the material.
- Compatible Materials: ISO 11114-4 prescribes test methods for selecting compatible steels resistant to Hydrogen embrittlement for fabrication of cylinders and valves.
High diffusivity in Air
Hydrogen diffuses very rapidly when released into the atmosphere. The diffusion rate of Hydrogen in air is almost 4 times that of air. This, coupled with the fact that it is completely colorless and odourless, poses a serious challenge when working in enclosed spaces. A dangerously explosive atmosphere can form very rapidly in absence of proper ventilation or exhaust.
- Lower Explosive Limits (LEL) Detection: All spaces where there is possibility of Hydrogen gas to accumulate and mix with air should be provided with % LEL detector. The lower explosive limit of Hydrogen in Air is 4% vol. Catalytic bead type LEL detector is the most common way to detect Hydrogen or any other explosive gas mixtures.
- Adequate Ventilation: Any space where Hydrogen can generate or leak should be provided with adequate ventilation. The ideal way to handle this challenge is to have the system outdoors whenever possible. Hydrogen’s high diffusion coefficient and its tendency to go upwards actually works to our advantage when the system is placed outdoors due to the absence of corners for significant gas pockets to be trapped.
Positive Thomson-Joule effect
Most gases, when released from a vessel of higher pressure, become cooler. However, Hydrogen exhibits Positive Joule-Thomson effect at temperatures above 193K, the inversion temperature. Thus, when Hydrogen is taken out of a pressurized vessel, it actually heats up. For a sudden pressure drop from 20MPa to ambient pressure, an instant temperature change up to 6 degC might be observed. This poses specific challenges in terms of possibility of rapid decompression as well as the Hydrogen fueling technologies.
- Slowing down the fueling Rate: The faster Hydrogen is evicted from a pressurized chamber, the higher the temperature rise is. This can be managed by slowing down the fueling rate so that the temperature doesn’t exceed ignition point at any part of there fueling system.
- Storage at lower temperatures: Under some circumstances, the above condition might limit the fueling rates to unfeasible low levels. In order to circumvent this, the gas can be precooled to sub-zero temperatures, so that even when temperature rises due to expansion, temperature at no point in the system exceeds the ignition limits.
Conclusion
Safety is a paramount concern when it comes to the generation and use of hydrogen.
All fuels have a certain amount of risk associated with their use. Hydrogen, due to its special properties, brings about some unique risks which can be mitigated effectively if specific protocols are in place for proper handling, processing, and storage of Hydrogen.
We, at Newtrace, implement state-of-the-art safety systems, rigorous testing regimes, and continuous monitoring of our Electrolyzer systems to ensure safe and efficient hydrogen production.
As the world continues to explore hydrogen as a clean energy source, safety will always remain our top priority. With a commitment to efficiency and best practices, we look forward to harnessing hydrogen as a safe and reliable energy solution, contributing to a sustainable and greener future.
Newtrace is enabling wide-scale adoption of affordable green Hydrogen through their novel electrolyzer technology to help fight climate change and build a sustainable future for all. Follow us to stay informed about our updates!